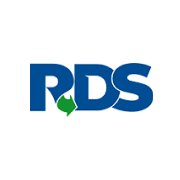
How RDS of Virginia increased recovery by 10% and brought consistency to its operations with AI-guided robotics
Sustained picks per minute per robot
Real Results
- 80
Sustained picks per minute per robot
- 98%
Accuracy of material identification and recovery
- 400
Feet per minute belt speed
“Our bottom line has improved drastically. It’s been an improvement in efficiency and you see a complete difference in the grade of the material, which helps you understand the function of the robots versus not having them.”
Recycling & Disposal Solutions (RDS) of Virginia provides commercial, residential, and industrial recycling services throughout southwest Virginia. The company’s two materials recovery facilities in Roanoke and one in Portsmouth process more than 4,500 tons of material each month.
Challenges:
Labor shortages, new quality standards impede profitability
Because of low unemployment levels in 2018, Joe Benedetto, president of RDS of Virginia, had a tough time finding the manpower to fully staff his operations—people who consistently came in on time every day and were up for the dusty task of manually sorting recyclable items from the waste stream. The difficulty of securing temporary workers was costly from the standpoint of money spent on staffing advertisements, often with little return, and from the time interviewing, onboarding, and training workers took away from other pressing tasks within the operation.
The arrival of stricter international quality standards for contamination-free imports of recycled materials exacerbated the challenges RDS faced around labor. The need to produce a cleaner, higher-quality bale without adding more people left small businesses like Joe’s searching for cost-effective alternatives to meet these new requirements.
The volatile cost of labor and market changes combined to make it extremely challenging to operate at a profit—and that was before the onset of COVID-19. In 2020, the pandemic brought a shift in volumes, with a sharp uptick in residential and a dropoff in commercial; changes to the material stream, like more fiber and single-use plastics, and increased contamination; and new protocols around personal protective equipment, cleaning, and social distancing in facilities where employees are accustomed to working in close proximity.
Solution:
AMP’s systems work with existing infrastructure
Joe, who had grown up around the recycling industry with a family history in the business dating back to the late nineteenth century, always recognized the benefits of technology and the need to make ongoing investments in his facilities to continue to improve the process. In mid-2019, following the chance to observe AMP’s systems operating in other facilities firsthand and see their edge over competing solutions, RDS installed four AMP Cortex intelligent robotics systems in one of its Roanoke facilities for quality control to remove plastic film, cups, metals and other contamination on its fiber line as well as for sorting PET and HDPE on its container line.
The units were dropped in with no changes to RDS’ existing infrastructure over a weekend, and without additional costs beyond the financing of the equipment. The only change RDS has implemented since installation is a daily maintenance inspection, a process that takes no more than 20 minutes, to ensure the hoses and suction cups are intact and the screens underneath the cups are clean. RDS proactively replaces the cups every other day to avoid any interruptions to its throughput and has had a smooth experience ordering any replacement parts through AMP’s customer service platform, which is part of the Extended Support plan AMP offers
Results:
Lower labor costs and new career paths
AMP’s technology helped RDS better manage its employee base, allowing the company to stabilize its sorting workforce and improve productivity. Joe retained all of his full-time employees following the addition of AMP’s systems, but he was able to eliminate temporary positions, along with the expenditure for advertisements for these roles, often with little return. Labor costs including screening and pre-employment tests, training expenses, workers’ compensation, personal protective equipment, and more can exceed tens of thousands of dollars per year for just a few employees; offsetting this figure with AMP’s technology translated not only to fewer injuries but a path to repayment within three to four years. Employing robots reduced RDS managers’ recruiting and onboarding workload by 20 hours per month and saved the company thousands of dollars each month.
RDS employees embraced their new coworkers. According to one employee interviewed, “Robots working side by side with humans—it’s a lot better. They may not catch everything, but humans can’t either! We need each other.” A manager elaborated, “Our bottom line has improved drastically. It’s been an improvement in efficiency and you see a complete difference in the grade of the material, which helps you understand the function of the robots versus not having them.”
Moreover, the addition of automation paved the way for RDS to create higher-skilled roles for its workforce. Joe hired an individual with a background in robot technology for a new management position and retrained one of his existing sort line employees, and paid him more, to help with daily maintenance on the robots. The robots are one of the easiest pieces of equipment RDS has to maintain; the skillset is one most operators can easily source from their existing staff or from a group already servicing a facility.
“As a MRF operator, this is one of the best investments you can make. There’s not another piece of equipment we could’ve purchased with the same impact. If I were starting a new facility, I wouldn’t do it without AI and robotics.”
Results:
A more profitable and resilient business
RDS is now profitable. This shift was driven by a pickup in commodity prices and RDS’ greater capacity to capture 10% more of these higher-value commodities with AMP’s technology. And Joe has a higher degree of confidence that he’ll maintain profitability with the cost stabilization robots provide over a longer time horizon, especially with a projected increase in the minimum wage. In addition to simplifying the operation, with AMP’s systems, RDS was able to preserve a lower cost model and make more competitive bids when proposing services to new customers.
When the pandemic hit, because RDS had already deployed AMP’s systems, the facility was in a strong position to weather the crisis.
RDS maintained full operations, and even added overtime, to handle the heavier volumes of recyclables driven by shelter-in-place orders and rapidly changing consumer behavior. It met demand for materials like paper and cardboard while protecting employees and controlling costs. Despite some employee absences, the robots allowed RDS to recover high volumes of recyclables to take advantage of demand pricing. Were it not for AMP’s automation, RDS may have needed two to four additional people to handle the greater volumes and contamination. But Joe didn’t have to add any headcount to increase processing capacity and material recovery, while limiting contamination to no more than 3%.
Looking ahead:
The tech-driven future of recycling
Joe has purchased additional AMP systems for his next project, now in design, and looks forward to what continuous improvements in AI and robotics will mean for operators like him: “With AMP’s technology, we can pick additional material we weren’t before because of the faster speeds and the ability of AMP’s AI to identify different materials in the stream. We’re extracting additional commodities, and getting a cleaner product because we’re removing contamination that might’ve slipped through in the past. The technology offers the flexibility for us to decide what we
want to sort as picks per minute increase. Plus, the AI platform learns and expands its scope over time, so we get smarter along with the system.”
AMP’s technology brought consistency to RDS’ operations, and that’s one of its greatest benefits. Operating a recycling facility comes down to a multitude of systems and processes, and robots were a piece of equipment that could be counted on to perform while remaining easy to manage.